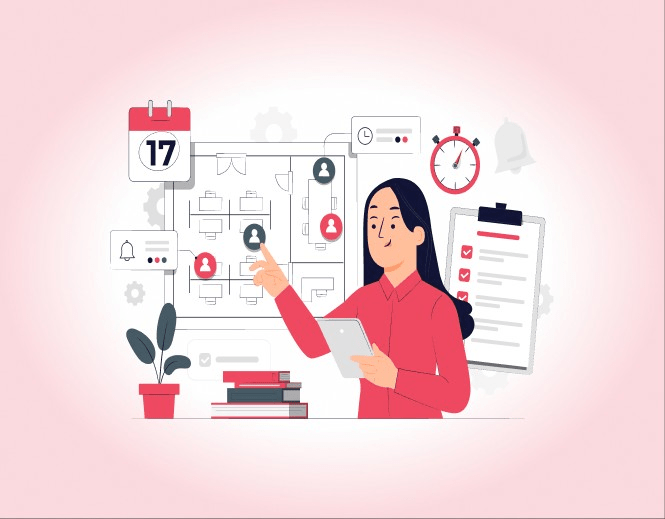
Home »
Implementing Lean Principles in Business Operations
Discover the transformative impact of implementing Lean principles in business operations.
Introduction
In today’s highly competitive business landscape, organizations strive to gain a competitive edge by maximizing efficiency and minimizing waste in their operations. To achieve these objectives, many companies are turning to Lean principles—a systematic approach that has proven to be highly effective in streamlining processes, reducing costs, and enhancing overall productivity. This article explores the implementation of Lean principles in business operations and the significant benefits they can bring.
Lean principles originated from the Toyota Production System (TPS) and have since been adopted and adapted by numerous industries worldwide. The core philosophy of Lean revolves around the elimination of non-value-added activities, known as waste, to create a leaner and more efficient operation. By identifying and eliminating waste, businesses can optimize their resources, enhance customer value, and ultimately boost their bottom line.
Implementing Lean principles requires a fundamental shift in mindset and a commitment to continuous improvement. It involves engaging employees at all levels of the organization, fostering a culture of collaboration, and empowering individuals to identify and address inefficiencies in their daily work. Lean principles encompass various tools and techniques, such as value stream mapping, 5S (Sort, Set in Order, Shine, Standardize, Sustain), Kanban systems, and Kaizen events, to name a few.
What are Lean Principles?
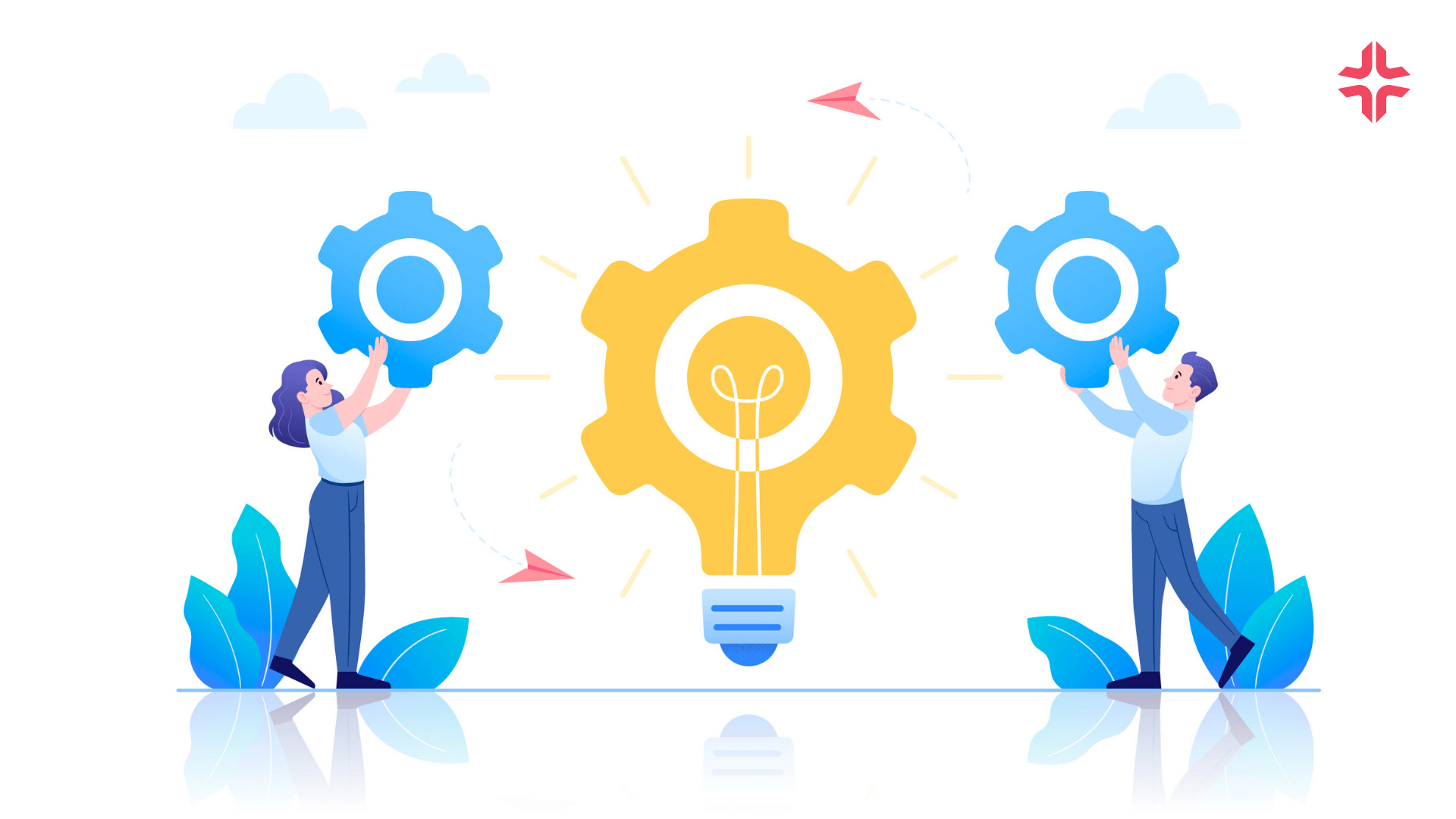
Lean principles are a set of fundamental concepts and practices aimed at optimizing business operations by maximizing efficiency and minimizing waste. Originally developed by Toyota in the manufacturing industry, these principles have since been adopted and implemented across various sectors and functional areas, ranging from healthcare to software development.
At its core, Lean is a customer-centric approach that focuses on delivering value while eliminating activities that do not contribute to that value. The overarching goal is to streamline processes, reduce costs, and enhance overall productivity. Lean principles emphasize continuous improvement, employee empowerment, and the elimination of non-value-added activities or “waste.”
One of the key tenets of Lean is identifying and eliminating different types of waste. These wastes, often referred to as the “8 Wastes,” include defects, overproduction, waiting, non-utilized talent, transportation, inventory, motion, and extra processing. By eliminating or minimizing these wastes, organizations can optimize their operations and enhance efficiency.
Another important principle of Lean is creating a culture of continuous improvement. This involves fostering a mindset of constant learning, experimentation, and problem-solving at all levels of the organization. Continuous improvement initiatives, such as Kaizen events and Lean Six Sigma projects, enable employees to identify inefficiencies, suggest improvements, and implement changes that lead to better outcomes.
Furthermore, Lean principles emphasize the importance of empowering employees and involving them in decision-making processes. Engaging frontline workers who are directly involved in the day-to-day operations can yield valuable insights and ideas for improvement. By empowering employees, organizations tap into their knowledge and expertise, which can result in more efficient processes and higher employee satisfaction.
Benefits of Lean Implementation
There are many benefits to implementing lean principles in your business. These benefits include:
- Increased efficiency and productivity
- Reduced costs
- Improved quality
- Increased customer satisfaction
- Increased employee morale
- Improved safety
- Reduced environmental impact
Increased Efficiency and Productivity | Lean principles streamline processes, eliminate waste, and enhance workflow, leading to higher efficiency and productivity. |
Reduced Costs | By minimizing waste and optimizing resource utilization, lean practices contribute to cost reduction and improved financial performance. |
Improved Quality | Lean methodologies emphasize quality control and error prevention, resulting in improved product and service quality. |
Increased Customer Satisfaction | Efficient processes, shorter lead times, and better quality contribute to enhanced customer satisfaction and loyalty. |
Increased Employee Morale | Engaging employees in lean practices empowers them to contribute ideas, fostering a sense of ownership and pride in their work. |
Improved Safety | Lean principles often involve safety considerations, leading to safer work environments and reduced workplace hazards. |
Reduced Environmental Impact | Minimizing waste and optimizing resources align with sustainable practices, reducing the organization’s environmental footprint. |
The Seven lean principles:
Lean principles provide a powerful framework for businesses to optimize their operations, enhance efficiency, and reduce waste. By incorporating these principles into their processes, organizations can improve customer satisfaction, streamline value streams, and achieve continuous improvement. This article explores the seven core lean principles and their significance in driving operational excellence.
The first principle is to specify value from the customer’s perspective. Understanding customers’ wants and needs is crucial for aligning business processes with their expectations. By tailoring products or services to meet customer requirements, companies can deliver superior value and enhance customer satisfaction.
The second principle involves identifying the value stream. This encompasses analyzing the sequence of steps involved in transforming raw materials into a final product or service. By mapping the value stream, organizations gain insights into areas of inefficiency and can focus on eliminating non-value-added activities.
Flowing the value stream is the third principle, emphasizing the elimination of unnecessary steps and delays. Streamlining the flow of work ensures smoother operations, reduces lead times, and minimizes bottlenecks. This principle encourages businesses to optimize their processes, enabling a more efficient and effective value delivery system.
The fourth principle is to pull value from the customer. Rather than producing goods or services based on forecasts or assumptions, this principle emphasizes producing only when the customer demands it. By aligning production with actual demand, organizations can reduce inventory costs and eliminate overproduction.
Pursuing perfection is the fifth principle and involves continually seeking ways to improve the value stream. By fostering a culture of innovation and encouraging employees to identify and address inefficiencies, businesses can strive for operational excellence and deliver higher value to customers.
Respect for people is the sixth principle, highlighting the importance of creating a work environment that values and empowers employees. When individuals feel respected and empowered, they are more motivated to contribute their ideas and efforts towards process improvement.
Finally, the seventh principle is continuous improvement. This principle encourages organizations to adopt a mindset of ongoing growth and development. By never settling for the status quo and consistently seeking ways to enhance processes, businesses can maintain a competitive edge and adapt to changing market conditions.
In conclusion, implementing lean principles in business operations offers significant benefits in terms of maximizing efficiency and minimizing waste. By aligning processes with customer value, streamlining value streams, empowering employees, and fostering a culture of continuous improvement, organizations can enhance their competitiveness and achieve sustainable success in today’s dynamic business landscape.
Specify value from the customer’s perspective. This means understanding what the customer wants and needs, and then designing your processes to deliver that value.
- Identify the value stream. This is the sequence of steps that transforms raw materials into a finished product or service.
- Flow the value stream. This means eliminating unnecessary steps and delays in the value stream.
- Pull value from the customer. This means only producing goods or services when the customer is ready to receive them.
- Pursue perfection. This means continuously looking for ways to improve the value stream.
- Respect for people. This means creating a work environment where people are valued and empowered to make decisions.
- Continuous improvement. This means never being satisfied with the status quo and always looking for ways to improve.
How to Implement Lean Principles in Your Business
There are many ways to implement lean principles in your business. The best approach will vary depending on the specific needs of your business.
However, there are some general steps that you can follow:
- Start by identifying waste. This can be done by mapping your value stream and looking for any steps that do not add value to the customer.
- Once you have identified waste, you can begin to eliminate it. This may involve making changes to your processes, tools, or equipment.
- As you eliminate waste, you will need to continuously monitor your processes to ensure that waste does not creep back in.
- Finally, you need to create a culture of continuous improvement. This means encouraging employees to identify and eliminate waste on a regular basis.
Some key steps to consider
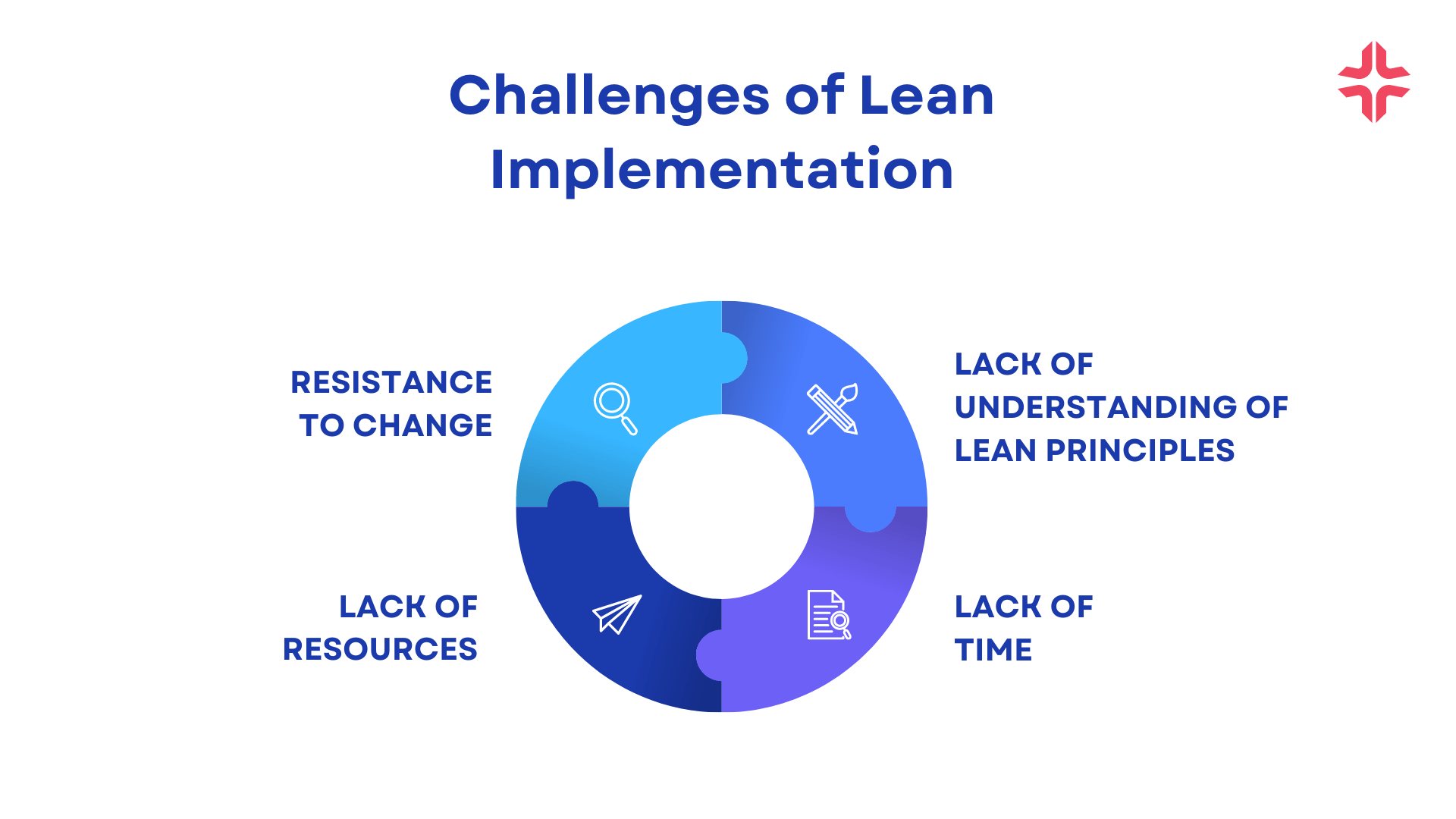
Challenges of Lean Implementation
Lean principles have gained widespread recognition as an effective approach to optimizing business operations. By maximizing efficiency and minimizing waste, organizations can streamline their processes and enhance overall productivity. If you’re looking to implement lean principles in your business, here are some key steps to consider:
- Understand the Lean Philosophy: Familiarize yourself with the core principles of lean, such as identifying value from the customer’s perspective, mapping the value stream, creating flow, establishing pull, and relentlessly pursuing perfection. This foundational knowledge will guide your implementation efforts.
- Identify and Eliminate Waste: Conduct a comprehensive assessment of your current operations to identify areas of waste. Waste can take various forms, including excess inventory, overproduction, unnecessary motion, defects, and waiting time. Once identified, develop strategies to eliminate or minimize these wastes to improve efficiency.
- Foster a Culture of Continuous Improvement: Lean is not a one-time initiative but rather an ongoing journey of continuous improvement. Encourage employees at all levels to actively participate in identifying problems, suggesting improvements, and implementing changes. Create a culture that values experimentation, learning, and adaptation.
- Implement Visual Management: Visual management techniques, such as visual boards, kanban boards, and visual indicators, can help make information transparent and easily accessible. These tools enable teams to understand the current state of operations, identify bottlenecks, and make data-driven decisions.
- Streamline Processes: Analyze your value stream and look for opportunities to streamline processes. Simplify workflows, reduce unnecessary steps, and standardize work procedures where possible. This can help eliminate non-value-added activities and enhance overall flow and productivity.
- Empower and Train Employees: Provide comprehensive training to employees on lean principles, tools, and techniques. Empower them to take ownership of their work areas and encourage their involvement in problem-solving initiatives. Invest in their professional development to build a capable and engaged workforce.
- Measure and Track Performance: Establish key performance indicators (KPIs) aligned with lean goals and regularly measure and track your progress. Monitor metrics such as cycle time, lead time, defect rates, and customer satisfaction. Use the data to identify areas that require further improvement and celebrate successes along the way.
Challenges of Lean Implementation
There are some challenges associated with implementing lean principles in your business. These challenges include:
- Resistance to change
- Lack of understanding of lean principles
- Lack of resources
- Lack of time
Manage resources effectively with KEBS
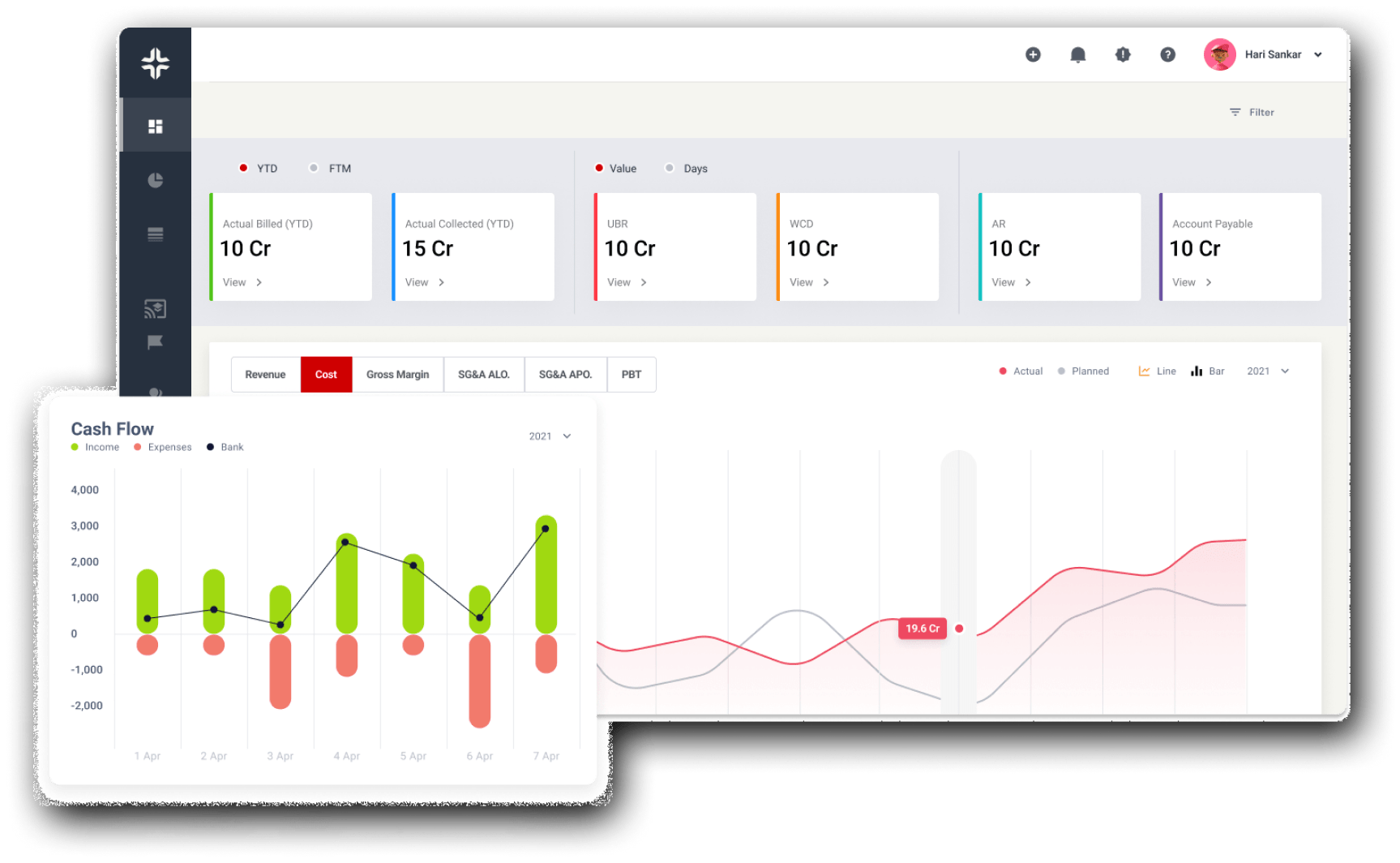
KEBS All in one PSA
Fix your revenue leakage and focus on productivity with an SaaS platform throughout your services lifecycle.
Here come KEBS
Manage resources effectively to deliver the best of outcomes even with limited availability. KEBS makes planning, organizing, and distribution of resources 2x easier.
- Project Management: KEBS assists businesses in planning, organizing, and monitoring projects effectively. It provides tools for creating project plans, assigning tasks, setting milestones, and tracking progress.
- Resource Management: With resource optimization as a priority, KEBS helps companies allocate resources, both human and otherwise, efficiently.
- Finance Management: KEBS likely includes features for managing the financial aspects of projects. This involves budgeting, tracking expenses, generating invoices, and recognizing revenue.
- Deal Management: For organizations with a sales component, KEBS may offer tools to manage the entire sales cycle.
- Ticket Management: If customer support is crucial to your business, KEBS might provide a system for effectively managing customer inquiries and support requests.
Project Management | Plan, organize, and monitor projects effectively. Create project plans, assign tasks, set milestones, and track progress with KEBS. |
Resource Management | Optimize resource allocation with KEBS. Efficiently allocate both human and other resources to maximize outcomes even with limited availability. |
Finance Management | Manage project finances seamlessly using KEBS. Budgeting, expense tracking, invoice generation, and revenue recognition are likely included features. |
Deal Management | Handle the entire sales cycle with KEBS, especially suitable for organizations with a sales component. |
Ticket Management | Efficiently manage customer inquiries and support requests with KEBS, especially useful for businesses prioritizing customer support. |
Conclusion
Lean principles can be a powerful tool for improving your business. By implementing lean principles, you can improve your efficiency, productivity, and profitability. However, it is important to be aware of the challenges associated with lean implementation and to take steps to mitigate these challenges.
Achieve 2x Growth with your projects and resources with KEBS