Home » PSApedia
Cycle Time
Manage Projects Efficiently with Shortened Cycle Time and Optimize Performance.
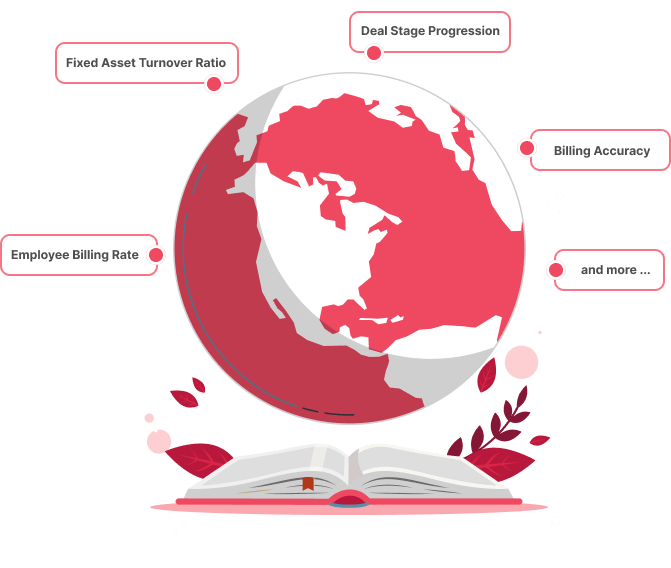
What Is Cycle Time?
Cycle time refers to the total time taken to complete a single task or operation from starting to finish. This measure provides insights into the efficiency of a particular process. In project management, it’s crucial to analyze it to improve workflows and enhance productivity.
To optimize this effectively, it’s essential to first conduct a comprehensive analysis of your existing processes. Identify areas where delays occur, whether because of manual tasks, equipment downtime, or inefficient workflows. Once you pinpoint bottlenecks, implement improvements such as automation, lean methodologies, and employee training to reduce better
Regular monitoring and adjustment of these strategies are vital for sustained success. Modern technologies such as data analytics and machine learning can provide real-time insights. These insights can improve processes and reduce further. Ultimately, this can lead to increased productivity and profitability.
Why Is Cycle Time So Important?
By constantly tracking and enhancing it, businesses can remain competitive, adjust to market changes, and ultimately increase their profits. So, in summary, the significance of cycle time lies in its ability to drive operational excellence and foster business growth. Understanding cycle time is essential for several reasons:
- Efficiency Evaluation: It aids organizations in identifying bottlenecks, thereby helping improve workflows.
- Cost Reduction: By optimizing processes, organizations can decrease cycle times, resulting in reduced costs.
- Customer Satisfaction: Shorter cycle times often lead to faster delivery, enhancing customer satisfaction.
Continuous improvement initiatives use it as a benchmark to streamline operations.
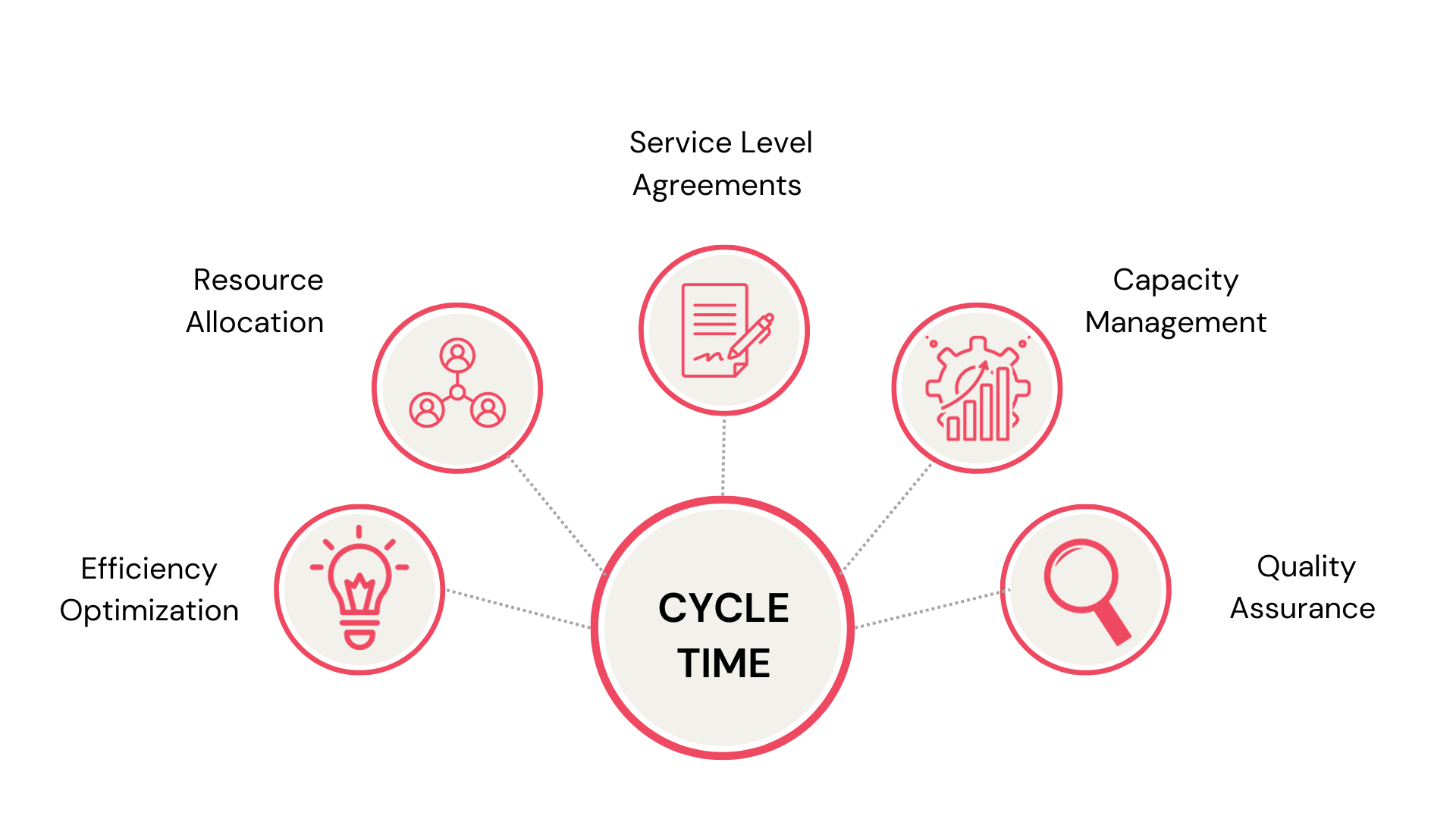
Why Is Cycle Time So Important?
Calculating Cycle Time
Calculating CT is a crucial aspect of process optimization in various industries. Whether in manufacturing, software development, or project management, understanding and efficiently determining cycle time can enhance productivity and reduce bottlenecks. The formula to calculate cycle time is quite straightforward:
Cycle Time = Production End Time – Production Start Time
If a ticket process starts at 10:00 AM and finishes at 2:00 PM, it takes 4 hours.
Differences Between Cycle Time and Lead Time
While it focuses on the time taken for a single task, lead time looks at the entire process. It’s the duration from receiving an order until its delivery. By understanding both, businesses can further optimize their deal management and overall operations.
Aspect | Cycle Time | Lead Time |
---|---|---|
Definition | The time it takes to complete one cycle of an operation or to produce one unit. | The time between the initiation and completion of a production process. |
Measurement | Starts when work begins on the item and ends when the item is ready for delivery. | Starts when a customer order is placed or a request is made and ends when the item is delivered or the request is fulfilled. |
Scope | Typically focuses on a specific stage or process. | Covers the entire process, from order to delivery. |
Components | Includes only the time when the work is actually being done. | Includes both the processing time and any waiting time. |
Usage | Useful for measuring efficiency within a specific part of the process. | Useful for understanding the overall time a customer must wait. |
Improvement | Improving cycle time often focuses on making a specific operation or task faster or more efficient. | Improving lead time can involve both reducing cycle time and reducing wait times between operations. |
Uses of Cycle Time in Real Time
It is ubiquitous across sectors:
- Manufacturing: Used to determine production efficiency and optimize machinery use.
- Software Development: Helps in evaluating the time taken to fix bugs or implement features, making tools like Gantt charts vital for tracking.
- Finance: Assesses the duration for processes like invoicing, a pivotal component in financial management.
- HR: Evaluates the time taken for recruitment or other employee-related processes, benefitting from tools such as employee 360 evaluations.
Are you ready to Optimize Your Cycle Time?
KEBS offers an array of solutions to businesses striving for operational efficiency. Its Professional Service Automation (PSA) software provides insights into processes, allowing for real-time adjustments. Utilizing its features, like timesheet billing, organizations can get granular details about their operations.
So, whether you’re aiming to decrease cycle times or improve your sales strategy, KEBS has the perfect solution.
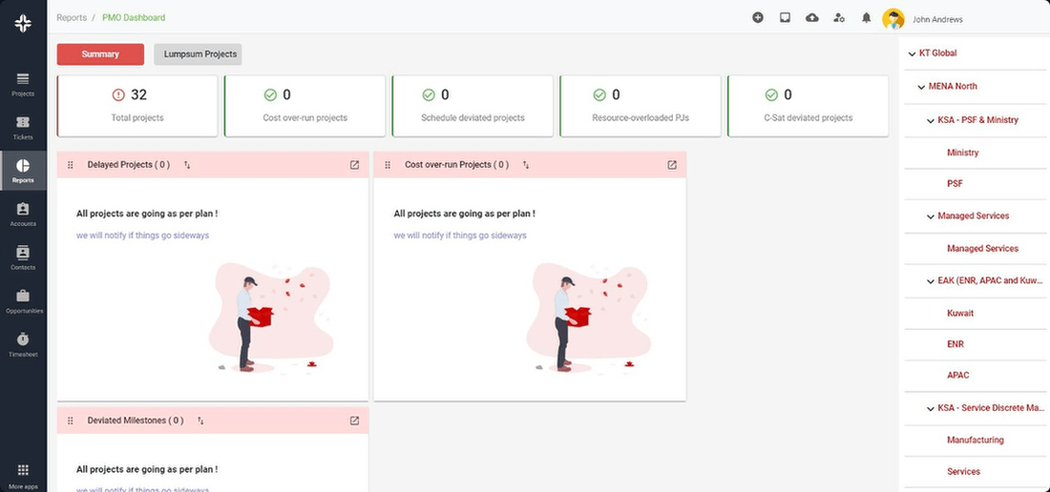
KEBS Project Management
Explore how KEBS can revolutionize your operations. for more details Contact us or request a demo to experience the KEBS advantage firsthand.